|
|
|
Best Practices Guides
Project Collaboration Best Practices
Case Studies - Cleveland Clinic Lutheran Hospital Emergency Department
PROJECT DESCRIPTION: A 29,000 SF renovation and expansion of a hospital emergency department in Cleveland, OH. The building that the ED occupies was built in 1957. The new emergency department will increase by 30% to 21 beds and 30,000 patients a year. With a primary focus on behavioral health patients, safety of patients, and giving care are first priority. Construction is scheduled for 22 months and eight (8) phases. The total building cost is $12,900,000 and the project was delivered under an Owner Controlled Team Project Delivery (OCTPD).
MAJOR IMPETUS FOR HIGHER LEVELS OF COLLABORATION: With the rising cost of healthcare and the increase in demand for patient services, the Emergency Department needed to be upgraded to continue operation. Two previously completed projects had cost overruns of 46% on average and schedule delays. The Hospital could not accept this level of risk on this size project.
KEY PLAYERS: OWNER: Cleveland Clinic; ARCHITECT: Bostwick Design Partnership; CONSTRUCTION MANAGER: The Krill Company
PROJECT TEAM SELECTION CRITERION: The Architect was selected on a proposal basis. The Owner and Architect selected the Construction Manager early in Schematic Design. Selection was based on a request for proposal and the interview. Together, the Owner, Architect, and CM selected Design- Assist trades during Design Development. Design-Assist trades included: electrical engineering, mechanical engineering, interiors, and fire protection. All Design-Assist trades were required to bid the job. The fire protection Design-Assist trade did not complete construction.
CULTURE AMONGST TEAM: The culture among the team is one of respect. Respect for each other and the Hospital grounds they are working within. The CM and Subcontractors have direct relationships with the Architect. Throughout the course of the project, surveys were completed to gauge the level of teamwork. Surveys included questions related to trust, respect, and cooperation. The team consistently scored 4.5 out of 5, with 5 being the highest.
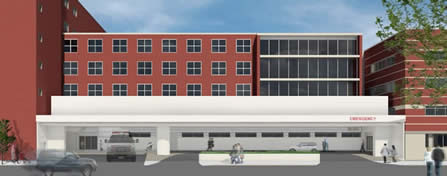
EARLY INVOLVEMENT OF PROJECT TEAM MEMBERS: This project team experienced an unprecedented level of commitment and engagement. The Owner and Architect selected the CM during Schematic Design. Design-Assist trades were selected early in Design Development. This engagement reduced the Owner’s risk to typical project budget and schedule creep. On this project, the budget set at Schematic Design is holding through construction. The entire team is actively engaged during both design and construction, increasing their understanding of the project. Throughout the course of the project, the team has improved their productivity, ultimately resulting in net savings to the job.
TECHNIQUES THAT ALLOWED TEAM TO OPERATE COLLABORATELY:
- OCTPD is an Owner led delivery method. The Owner was a key stakeholder representative at all design and construction meetings. The facilities department coordinated with the design and construction teams with regards to the existing facility.
- A Project Coach was hired to facilitate a Team Development process. This process allowed the team to create a common mission and project specific goals. The team created unique action plans to achieve project goals. Together they monitored progress and remained focused on the aforementioned project-specific goals during construction.
- Multi-discipline task teams were deployed to track progress on goals and solve specific problems as necessary. This task team approach created the opportunity for the appropriate team member to be involved in the solution. Additionally, it added to the complete transparency of the project status by all entities involved in the project team.
RESOURCES THAT ENHANCED COLLABORATION:
- BIM was used as a communication tool. Models and details were shared during design. Existing conditions were modeled and the BIM model was used to proactively work through field conditions, identify conflicts, and share knowledge.
- Old-fashioned, standard conversations were used. Every key team member had headquarters within ten miles of the job site. The team capitalized on this proximity during design and construction as face-to-face meetings were held with little advanced noticed, often to get to an immediate solution or to keep team members informed of progress.
QUANTIFIABLE PROJECT OUTCOMES:
- The project budget established at the conclusion of Schematic Design has held through 70% completion of construction. The team does not see that this will change.
- 96% of the construction contingency remains unused.
- Changes during construction have resulted in a savings (give back) to the project budget.
- Rework due to unforeseen conditions has been less than $5,000. This is unprecedented for renovating a 1957 building.
- Patient satisfaction scores have increased during construction.
- There have been no recordable safety infractions through 70% construction completion.
LESSONS LEARNED FROM THIS PROJECT: The project had four major goals: maintain patient/staff/team satisfaction, manage the budget and schedule, keep leadership engaged and informed, and make decisions with the entire hospital in mind. The key lessons learned for each are as follows:
- Maintain Patient/Staff/Team Satisfaction: When working within an existing hospital, it is critical to keep the patients and staff informed on the impact of the construction project. To do this, we notified staff verbally during their hospital daily safety huddles, and we sent out weekly newsletters highlighting the upcoming work and noise level. These two things allowed the caregivers to not be surprised by the level of activity. The team made an improvement by allowing for more time for staff to move into space before opening. We made an adjustment to the schedule Phases 2-5 after Phase 1 opening resulted in frustrated staff.
- Manage Budget and Schedule: The key to this was two-fold: full transparency and compartmentalizing budget and schedule into small manageable parts. Our team focused on eliminating rework from unknown conditions and Owner changes. To manage unforeseen conditions, the Architect partnered with Design-Assist trades to complete an invasive existing conditions review. This investigation during design, coupled with using BIM, allowed the team to effectively manage existing conditions. One lesson learned was to model all existing conditions. The team made a decision to not include an area in the model during design, this area proved to be the most difficult to build. Building a visually effective design model which accurately represented the clinical spaces allowed the Owner to understand their new working conditions. Reviewing 3D design with the clinical team, once again, just before construction, proved to be beneficial to both budget and schedule.
- Keep Leadership Engaged and Informed: The construction team developed a customized monthly reporting system that detailed the budget and schedule, highlighting specific goals; such as: contingency spent, rework, changes, and RFIs. This consistent and transparent report allowed leadership to make informed project decisions. The leadership team from all project partners were are engaged in regular jobsite rounding sessions as a result. These sessions mirrored clinical rounds by physicians and allowed the team to gauge the status of the project. Rounding occurred every two weeks during the twenty-two month project.
- “Make Decisions With The Entire Building In Mind”: The construction team was able to coordinate critical shutdowns and temporary heating/cooling without impacting patient care. Additionally, the construction team was able to stop and rework their schedule without impact to the project schedule or budget when exterior work impacted and caused vibration of the operating room.
AIA-MBA Joint Committee Contact Information:
Eric Starkowicz, Director of Industry Relations, Master Builders’ Association of Western PA
Phone: 412.922.3912 Email: estarkowicz@mbawpa.org
|
|